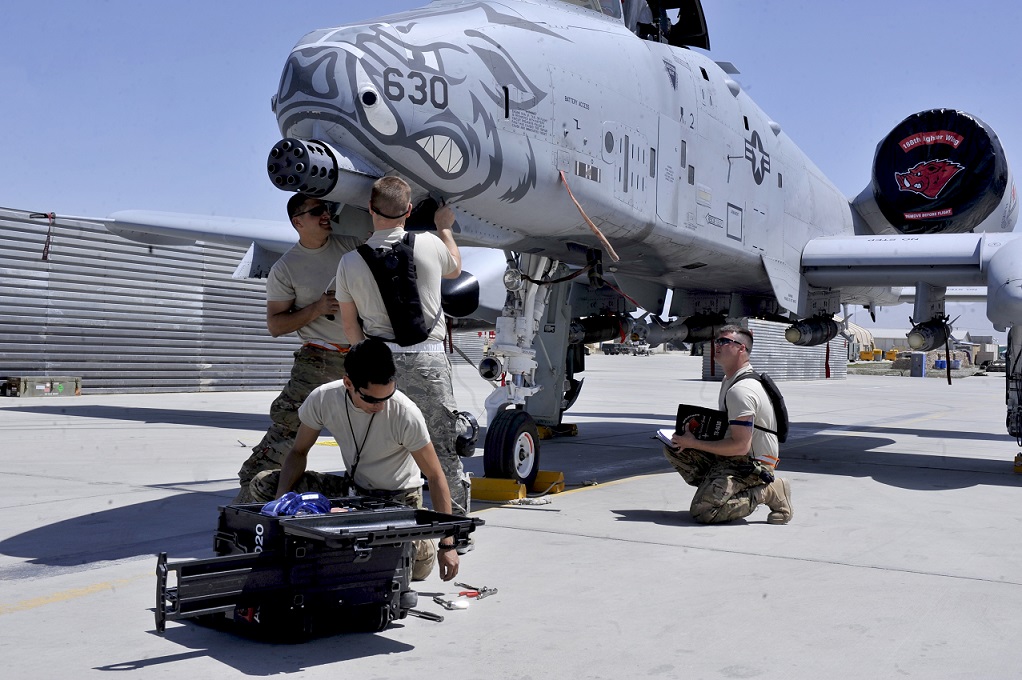
This post is also available in:
עברית (Hebrew)
Advancements in technology are spurring US Special Operations Command to examine how it can improve its artificial intelligence capabilities on a data-driven battlefield. One of the areas is predictive maintenance, logistics, planning and forecasting. Predictive maintenance allows us to get ahead of equipment failures, by helping determine the condition of in-service equipment in order to estimate when maintenance should be performed.
The Special Operations Command is crafting a new artificial intelligence and machine learning strategy. David Spirk Jr., the organization’s chief data officer, said: “Data-driven technologies can be used in every function that we have,” he told nationaldefensemagazine.org. “We hope to demonstrate the capability and then allow that to just grow in the services where, naturally, it should.”
Other examples of predictive maintenance refer to a wide range of air and ground systems. The US Air Force has been looking at new technologies to improve readiness and decrease maintenance downtime. This includes additive manufacturing, such as 3-D (spare part) printing, as well as analytics that use vast amounts of data to create models that can predict when an aircraft’s part is likely to break, instead of waiting for it to fail.
According to airforcetimes.com, one predictive maintenance program, known as conditions-based maintenance, is expected to cut the number of unscheduled maintenance events. It will allow maintainers and operators to decide when and where the maintenance should be performed.
Defense Innovation Unit (DIU), the Defense Department’s rapid prototyping organization, is working with C3, a company specializing in AI to aggregate and keep current enormous volumes of disparate data, including sensor reports and maintenance logs, in a unified cloud-based data image running on the GovCloud solution from AWS – Amazon Web Services.
The project initially focused on the F-16 fighter jet and the E-3 Sentry Airborne Warning and Control System. It uses AI to reduce maintenance costs and can be expanded for use on vehicles of all kinds. “That’s a huge opportunity, saving potentially billions of dollars as you apply what’s already in use in the commercial airline space to military aircraft,” he adds. “We’re now expanding it to other types of aircraft and the Bradley Fighting Vehicle. We’re working with all three branches—Army, Air Force and Navy.”
Another project is the Kessel Run project with the Air Force. In the past, Air Force personnel organized aerial refueling missions by entering mission data on an Excel spreadsheet and visualizing that data by drawing lines with dry-erase markers and arranging magnets to organize each day’s mission. Coders from DIU rapidly developed a program that allows one person to accomplish in three hours a task that once took a six-person team eight hours, according to afcea.org.